Within the ever-evolving world of materials science, the development of new substances can lead to groundbreaking applications across different industries. One notable material that has gained considerable attention is PI plastic, a multi-faceted and high-performance polymer known for its distinct properties. PI plastic, also known as polyimide resin material, showcases exceptional thermal stability, chemical resistance, and mechanical strength, making it a key choice for engineers and manufacturers seeking effective solutions for demanding environments.
The journey of PI plastic from theory to realization is a demonstration to the innovation of the science of materials. Utilizing advanced processes in PI engineering of plastics, researchers and engineers have transformed concepts into physical products. This process not only illustrates the technical challenges involved in creating high-performance materials but also illustrates the potential applications in industries such as electronics, aerospace, and automotive field. As we investigate the development of PI plastic, we will uncover how it has revolutionized the way we tackle complex engineering challenges and the exciting future that lies ahead for this exceptional material.
Comprehending PI Plastic
PI Plastic, made from a polyimide-based resin, is a premium engineering material recognized for its outstanding heat resistance and mechanical properties. Thanks to its unique composition that enables it to preserve its properties at high temperatures, PI Plastic is often selected for uses that require strength and consistency under challenging environments. This makes it as an excellent material for sectors such as aerospace, electronics, and vehicle manufacturing, where functionality is essential.
A key characteristic of PI Plastic is its superior chemical stability. It can endure exposure to a variety of solvents, fuels, and substances, making it ideal for use in conditions where other plastics may break down. Such a quality not only increases the durability of elements but also ensures that they work efficiently over time. As a result, PI Engineering Plastics have turned into a popular choice in uses that require strict material performance.
The flexibility of this engineering plastic is additionally improved by its potential to be processed into multiple configurations such as thin layers, panels, and molded parts. This adaptability allows manufacturers to create parts tailored to specific requirements and applications. Be PI Material used in insulation applications, structural parts, or as a part in complex assemblies, PI Plastic offers a reliable solution that meets the challenging needs of contemporary engineering obstacles.
Applications of Polyimide Resin
PI resin is well-known for its exceptional heat resistance and electrical insulation, making it an ideal choice in a variety of highly efficient applications. In the aircraft manufacturing, these materials are often used to fabricate components that must withstand harsh heat and challenging environments. Their lightweight nature combined with excellent mechanical properties allows for the fabrication of parts that enhance overall fuel efficiency and dependability in aircraft systems.
In the electronics industry, polyimide materials are used in the manufacturing of flexible printed circuits, where they serve as insulation layers that guard against high temperatures and electrical conductivity. Their ability to maintain performance in elevated temperatures makes them crucial in consumer electronics, telecommunications, and the automotive sector. These materials ensure longevity and dependability in devices that demand high performance under stressful conditions.
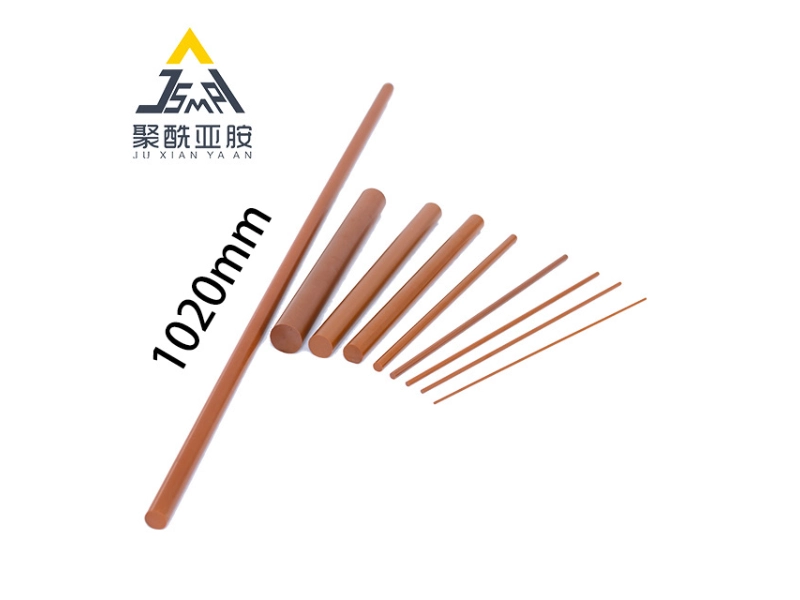
The medical field also benefits from polyimide resin, particularly in the development of specialized devices and devices. The biocompatibility and ability to be sterilized of polyimide materials make it appropriate for applications such as medical instruments and implants. As the demand for advanced healthcare technology continues to grow, the adaptability of polyimide resin showcases its potential to contribute substantially to cutting-edge healthcare solutions.
Benefits of Polyimide Engineering Plastics
Polyimide engineering plastics provide exceptional heat stability, enabling them appropriate for high-temperature contexts. Differently from conventional materials that may degrade or lose their structural integrity when subjected to elevated temperatures, polyimide resin preserves its properties despite extreme temperature levels. This feature is notably significant in industries such as aerospace and electronics, where devices must operate consistently under harsh circumstances.
Additionally significant advantage of PI technological materials is their superior resistance to chemicals. These materials are inherently immune to a wide range of chemicals, including thinners, corrosives, and alkalis, which makes them perfect for use in harsh settings. This durability enables manufacturers to employ polyimide plastics in instances that would typically pose a threat to standard plastics, thus ensuring long-term use and functionality in demanding contexts.
Moreover, polyimide engineering plastics show excellent electrical insulation characteristics. This feature is vital for the electrical engineering industry, where insulating materials are needed to eliminate short circuits and safeguard safe operation of equipment. The mix of thermal stability, chemical durability, and insulating properties renders PI plastics a versatile option, facilitating developments across multiple sectors while satisfying rigorous performance standards.
The Future of Polyimide Plastic Technology
As the demand for advanced materials continues to grow across various industries, the future of PI Polyimide Plastic technology looks promising. PI resin material is already recognized for its exceptional thermal stability, chemical resistance, and mechanical properties. As industries seek to innovate and improve productivity, PI plastic is expected to play a crucial role in applications such as aerospace, electronic devices, and automobile sectors. The versatility of PI engineering plastics will likely lead to wider applications and increased adoption.
Improvements in manufacturing techniques and material formulations are set to enhance the capabilities of PI Plastic. Researchers are exploring ways to develop new materials that further improve the mechanical strength and thermal properties of polyimide resins. By integrating intelligent technology and sustainable practices, the production of PI Polyimide Plastic could contribute to eco-friendly solutions while maintaining the necessary requirements required for high-performance applications.
Additionally, as industries push for miniaturization and weight reduction, PI Plastic will become increasingly essential. Their lightweight yet durable characteristics make them ideal for use in compact designs without compromising performance. This shift towards smaller, more efficient designs will likely drive innovations in Polyimide Plastic technology, leading to the development of next-generation materials that meet the evolving demands of modern engineering challenges.